In the world of heavy machinery, the term "Girthmaster" often emerges as a key topic of discussion when exploring robust and reliable components. If you're curious about the thickness and capabilities of Girthmaster, you're not alone. Engineers, project managers, and industry professionals frequently seek detailed insights into its specifications and applications. This article delves into the significance of Girthmaster, exploring its thickness, functionality, and importance across various sectors.
Girthmaster serves as a fundamental component in industries such as construction, mining, and manufacturing, ensuring the strength and reliability of machinery. Its design and specifications are carefully engineered to meet the demands of high-stress environments, making it an essential element in a wide range of applications. Understanding the thickness of Girthmaster is critical for anyone involved in the procurement and maintenance of heavy-duty equipment. This factor significantly influences the overall performance and durability of the machinery it supports.
This comprehensive guide aims to provide a detailed overview of Girthmaster, including its dimensions, materials, and performance metrics. By the end of this article, you will have a thorough understanding of why Girthmaster is highly regarded in the industry and how its thickness contributes to its effectiveness, enhancing the efficiency and longevity of heavy machinery.
Read also:Discover The Allure Of Sebring A City Where History Meets Adventure
Content Overview
- What Exactly is Girthmaster?
- Exploring the Thickness of Girthmaster
- Materials Utilized in Girthmaster
- Applications of Girthmaster Across Industries
- Advantages of Utilizing Girthmaster
- Comparing Girthmaster with Other Products
- Maintenance Guidelines for Girthmaster
- Cost Analysis of Girthmaster
- Industry Standards and Compliance
- Emerging Trends in Girthmaster Technology
What is Girthmaster?
Girthmaster refers to a specialized component used in heavy machinery and equipment, designed to provide structural support and stability in high-stress environments. It plays a crucial role in industries such as mining, construction, and manufacturing due to its ability to withstand extreme conditions. Understanding the role of Girthmaster is essential for anyone involved in the procurement and maintenance of heavy machinery.
Gaining insight into Girthmaster's function is vital for ensuring the durability and reliability of equipment. It minimizes the risk of failure in critical applications, contributing to safer and more efficient operations. The term "Girthmaster" encompasses a wide range of products, each tailored to meet specific needs. These components are manufactured using advanced materials and cutting-edge technologies, ensuring compliance with the highest industry standards.
As we explore further, we will uncover the various aspects of Girthmaster, including its thickness, materials, and applications, providing a comprehensive understanding of its significance in modern industrial operations.
Examining the Thickness of Girthmaster
The thickness of Girthmaster varies depending on the specific application and industry requirements. On average, Girthmaster components range from 10mm to 50mm in thickness, with custom designs often exceeding these dimensions. The exact thickness is influenced by several factors, including load capacity, environmental conditions, and material properties.
Key Factors Affecting Thickness:
- Load-Bearing Capacity
- Environmental Exposure
- Material Composition
- Industry Standards
For example, Girthmaster used in mining operations requires a thicker profile to endure heavy loads and abrasive conditions. In contrast, Girthmaster used in construction might feature a thinner profile while still maintaining its strength and durability. Understanding these variations is crucial for selecting the appropriate Girthmaster component for specific needs.
Read also:Yellowstone Season 5 Part 2 A Deep Dive Into The Dutton Family Saga
Thickness Variations by Industry
Let's explore how the thickness of Girthmaster varies across different sectors:
- Mining: Typically ranges from 30mm to 50mm
- Construction: Ranges from 10mm to 30mm
- Manufacturing: Custom designs available, often exceeding 40mm
Recognizing these variations is essential for making informed decisions when selecting Girthmaster components that align with your specific requirements.
Materials Used in Girthmaster
The materials used in the construction of Girthmaster are carefully selected to ensure optimal performance and longevity. Common materials include:
- High-Strength Steel
- Aluminum Alloys
- Composite Materials
High-Strength Steel is the most widely used material due to its exceptional load-bearing capacity and resistance to wear and tear. Aluminum alloys offer a lighter alternative without compromising strength, while composite materials are gaining popularity in certain applications for their superior durability and resistance to corrosion.
Each material has its own set of advantages and disadvantages, emphasizing the importance of selecting the right material based on the specific demands of the application.
Applications of Girthmaster Across Industries
Girthmaster finds extensive use across a broad spectrum of industries, including:
- Mining: Used in conveyor systems and heavy machinery
- Construction: Integral to cranes and excavators
- Manufacturing: Utilized in production lines and assembly equipment
In the mining sector, Girthmaster ensures the stability of conveyor systems, reducing downtime and enhancing operational efficiency. In construction, it provides the necessary support for cranes and excavators, enabling them to handle heavy loads with ease. In manufacturing, Girthmaster contributes to the precision and reliability of production lines, improving overall productivity.
Custom Applications of Girthmaster
Beyond standard applications, Girthmaster can be customized to meet unique requirements. These customizations include:
- Special Coatings for Enhanced Corrosion Resistance
- Custom Dimensions to Fit Specific Machinery
- Integrated Sensors for Real-Time Monitoring
These customizations enhance the functionality and effectiveness of Girthmaster, making it a highly versatile solution suitable for various industrial needs.
Benefits of Using Girthmaster
There are numerous advantages to incorporating Girthmaster into heavy machinery and equipment:
- Enhanced Durability: Girthmaster is designed to withstand extreme conditions, ensuring prolonged performance.
- Improved Efficiency: By providing structural support, Girthmaster reduces downtime and boosts productivity.
- Cost Savings: The extended longevity and reliability of Girthmaster translate into reduced maintenance and replacement expenses.
These advantages make Girthmaster an attractive investment for businesses aiming to optimize their operations and minimize costs.
Comparing Girthmaster with Other Products
When compared to other products in the market, Girthmaster stands out due to:
- Superior Strength: Girthmaster can accommodate higher loads compared to many competitors.
- Corrosion Resistance: Special coatings and materials ensure Girthmaster remains effective even in harsh environments.
- Customization Options: Girthmaster can be tailored to meet specific requirements, offering a competitive edge.
While other products may offer similar features, Girthmaster's combination of strength, durability, and customization capabilities makes it a top choice across numerous industries.
Key Differentiators of Girthmaster
What sets Girthmaster apart from its competitors?
- Advanced Material Composition
- Innovative Design Features
- Proven Track Record in Demanding Environments
These differentiators highlight why Girthmaster is a preferred option for professionals in the heavy machinery sector.
Maintenance Guidelines for Girthmaster
To ensure the longevity and optimal performance of Girthmaster, regular maintenance is essential. Below are some key maintenance tips:
- Regular Inspections: Monitor for signs of wear, corrosion, or damage.
- Lubrication of Moving Parts: Ensure all components are adequately lubricated to minimize friction.
- Adherence to Manufacturer Guidelines: Follow the recommended maintenance schedule and procedures diligently.
Implementing these maintenance practices will maximize the lifespan of Girthmaster and ensure it continues to perform at its best.
Cost Analysis of Girthmaster
The cost of Girthmaster varies based on factors such as size, material, and customization requirements. Typically, Girthmaster components range from $500 to $5,000, with custom designs exceeding these prices. While the initial investment may seem significant, the long-term benefits of using Girthmaster often outweigh the costs.
Factors Influencing Cost:
- Material Selection
- Customization Requirements
- Quantity and Lead Time
Purchasing high-quality Girthmaster components can result in substantial cost savings over time due to reduced maintenance and replacement needs.
Industry Standards and Compliance
Girthmaster must comply with various industry standards and regulations to ensure safety and optimal performance. Key standards include:
- ISO 9001: Quality Management Systems
- ASME B30.2: Specifications for Cranes and Hoists
- EN 1090: Execution of Steel Structures
These standards guarantee that Girthmaster components meet the highest levels of quality and safety, providing peace of mind to users.
Importance of Compliance with Industry Standards
Compliance with industry standards is crucial for several reasons:
- Ensures Safety and Reliability
- Facilitates International Trade and Acceptance
- Reduces Liability and Legal Risks
By adhering to these standards, manufacturers of Girthmaster can ensure the performance and safety of their products, maintaining trust and confidence among users.
Emerging Trends in Girthmaster Technology
The future of Girthmaster technology is promising, with advancements in materials and design leading to enhanced performance. Key trends include:
- Lightweight Materials: The development of lighter yet stronger materials to improve efficiency.
- Smart Components: Integration of sensors and IoT technology for real-time monitoring and analysis.
- Sustainability: A focus on eco-friendly materials and sustainable manufacturing processes.
These trends will shape the future of Girthmaster, making it an even more valuable asset for industries globally.
Emerging Innovations in Girthmaster
As technology continues to evolve, keep an eye on these emerging innovations:
- 3D Printing for Customized Components
- Advanced Coatings for Enhanced Durability
- Artificial Intelligence for Predictive Maintenance
These innovations will further enhance the capabilities of Girthmaster, setting new benchmarks in the heavy machinery industry.
Conclusion
In summary, understanding the thickness and overall significance of Girthmaster is just one aspect of its critical role in the heavy machinery industry. From its robust materials to its diverse range of applications, Girthmaster plays a pivotal role in ensuring the strength and reliability of equipment. By investing in high-quality Girthmaster components, businesses can optimize their operations and achieve long-term cost savings.
We encourage you to leave a comment or share this article with others who may find it insightful. For more information on heavy machinery and equipment, explore our other articles on our website. Together, let's stay informed and remain at the forefront of the ever-evolving world of technology and industry.

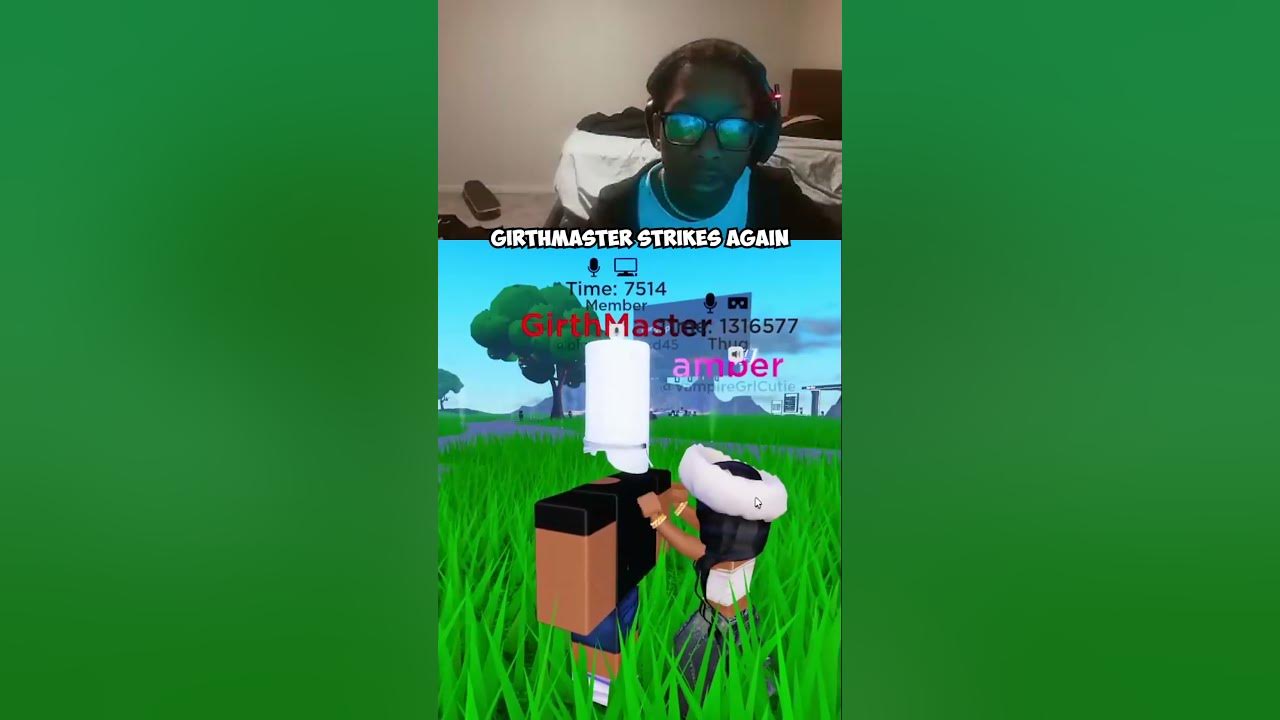
